Kornelis’ new laboratory takes injection molding to the next level.
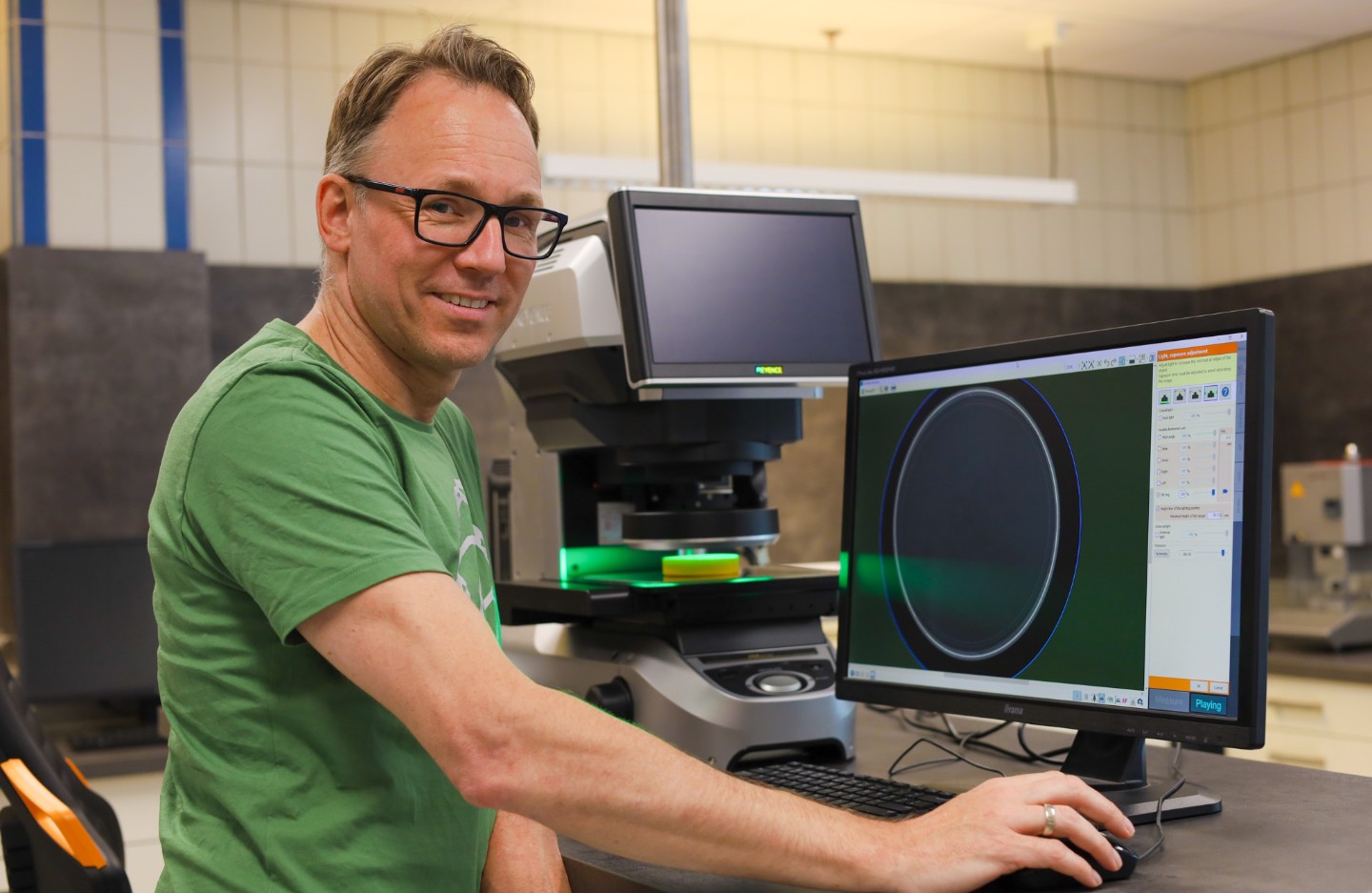
At Kornelis Caps & Closures in Steenwijk, innovation goes hand in hand with sustainability. This family-owned company, specialized in plastic caps and closures, recently upgraded its in-house laboratory to further improve production support.
"With data, we’re gaining more control over the process," says Mireia Mayol Orga, Process Engineer. Peter Gols, Senior R&D at Kornelis, adds: "Thanks to the new lab, we can measure much more accurately — not just the dimensions of the caps, but also the thickness of the sealing foil and the force needed to open flip-top caps. We can also detect sooner when a mold needs maintenance."
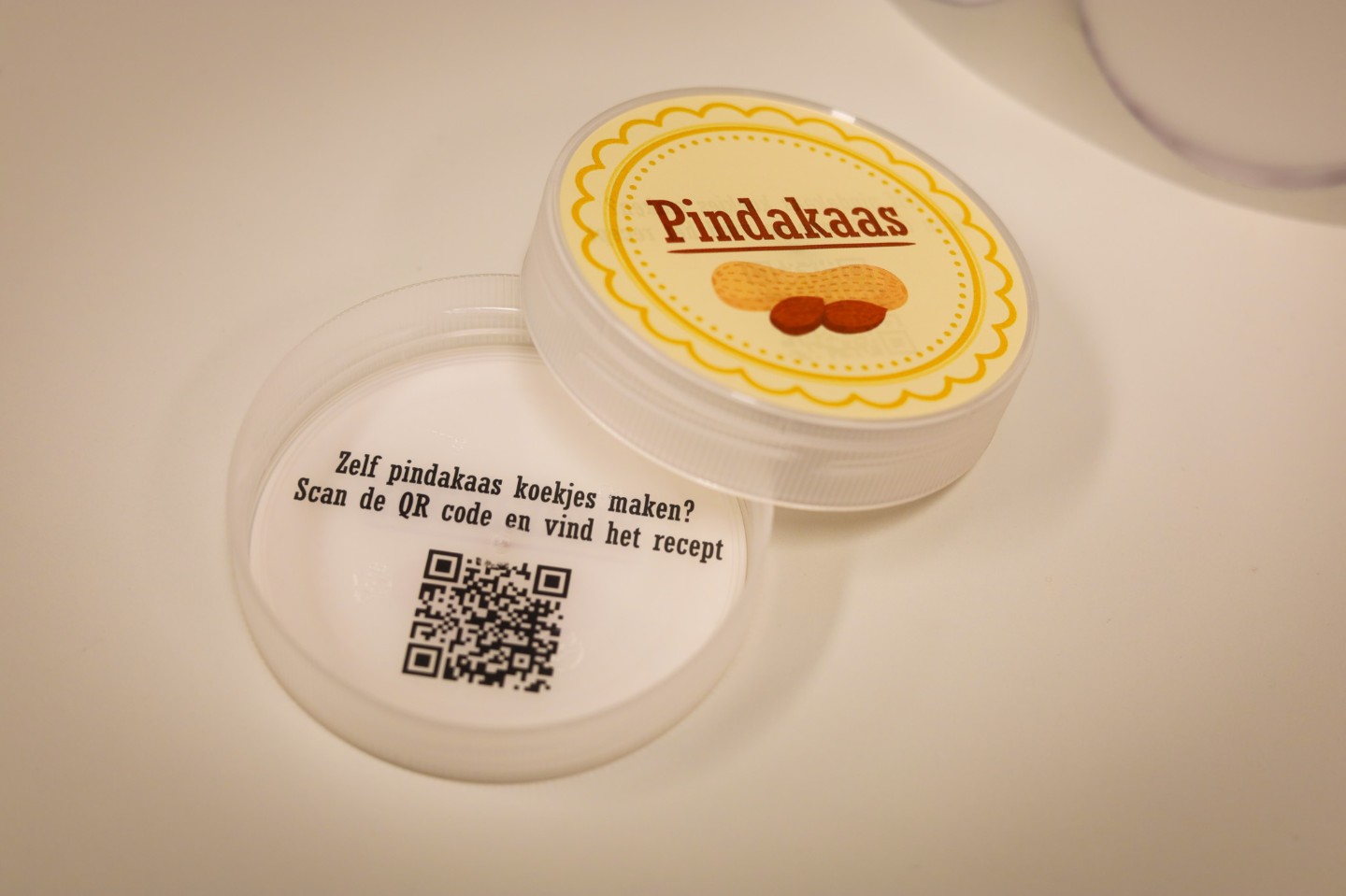
From caliper to measuring bench
In recent years, Kornelis has significantly modernized its measurement methods. In the past, quality checks were often done visually or with a caliper, which led to variations in measurements. Today, the lab is equipped with an optical measuring bench that quickly and accurately checks caps for thread quality, inner diameter, and bottom or tamper-evident edges. "Each cap is measured in exactly the same way," explains Peter. "This makes the process more consistent and helps us detect issues earlier." He gives an example: when measuring the force needed to open flip-top caps, a drop in that value can indicate contamination or wear in the injection mold. "Thanks to these measurements, we catch deviations much sooner."
A more stable injection molding process
The new measuring equipment also supports Kornelis’ goal of making the injection molding process more data-driven. "We're developing digital molding programs that calculate the ideal settings based on temperature, pressure, cooling time and other variables," says Peter. One trial involved a problematic machine and mold that used to break down frequently. "We optimized the setup and let it run for a full month," Peter says. "There wasn’t a single defect. That confirmed we’re heading in the right direction."
"We want to be able to measure and improve everything”
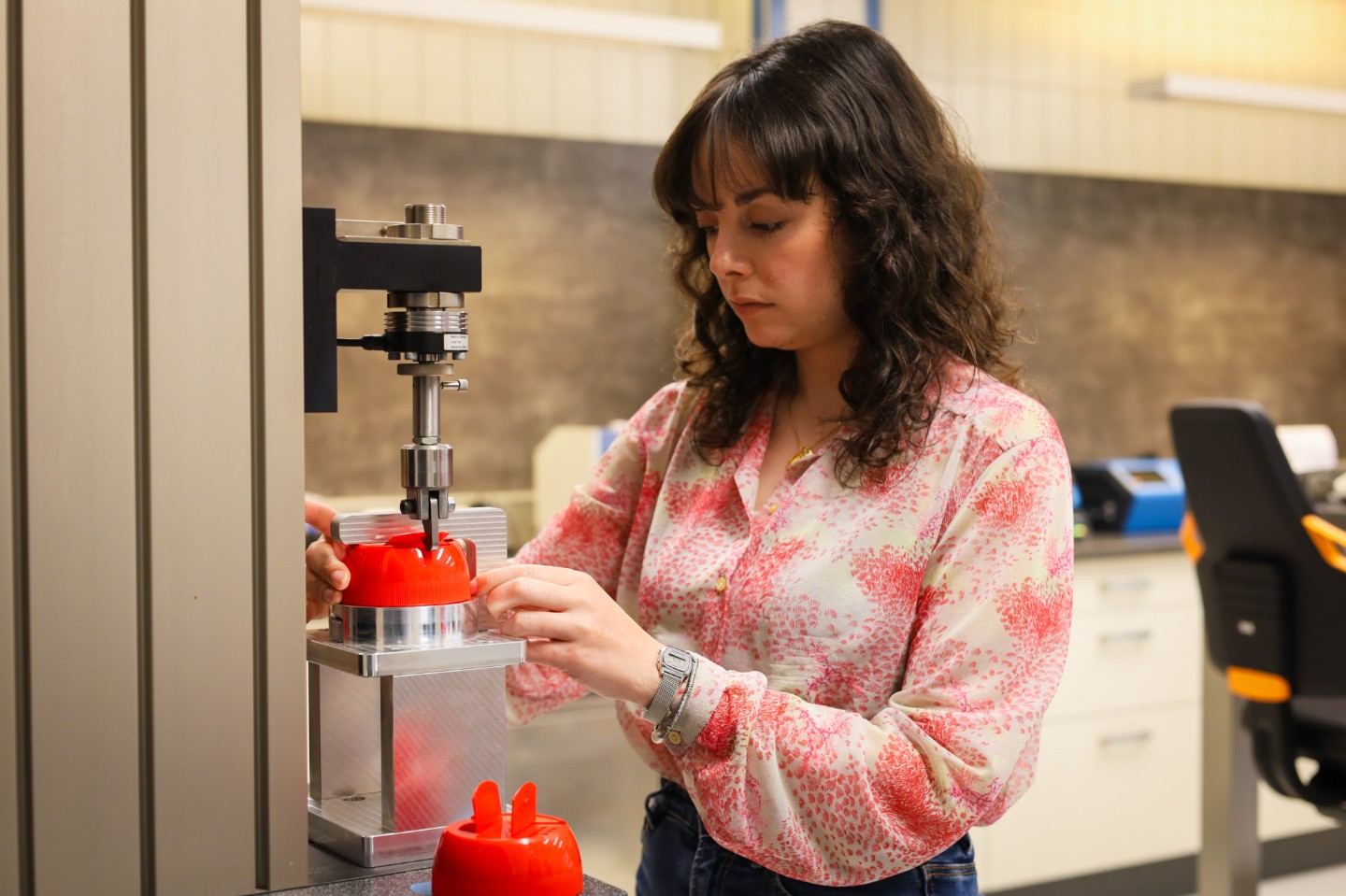
Self-correcting machines
Kornelis’ newest injection molding machines are equipped with servo drives and advanced software. They automatically adjust if the plastic flows slightly differently or if the properties of color additives change. "The machine checks whether everything stays within tolerance and corrects itself if needed," explains Mireia. "In the past, each operator relied on their own judgment when setting up the machine. Now, data supports the best program, helping us deliver consistent quality." Peter adds that the molds themselves are also improving. "Modern coatings reduce friction, so we need less lubricant in the plastic. That supports our goal of avoiding unnecessary substances in our products."
The impact of color and additives
The team has now fully analyzed how colorants affect the injection molding process. Some pigments cause more or less shrinkage, for example. "With green, we saw slightly larger caps; with white, they were smaller," says Mireia. "That means we need to adjust the settings or even use a different mold."
The aim is to minimize adjustments during color changes. "Fewer adjustments mean less waste and higher efficiency. Eventually, we want to switch colors without needing extra setup time or risking quality issues," Mireia concludes.
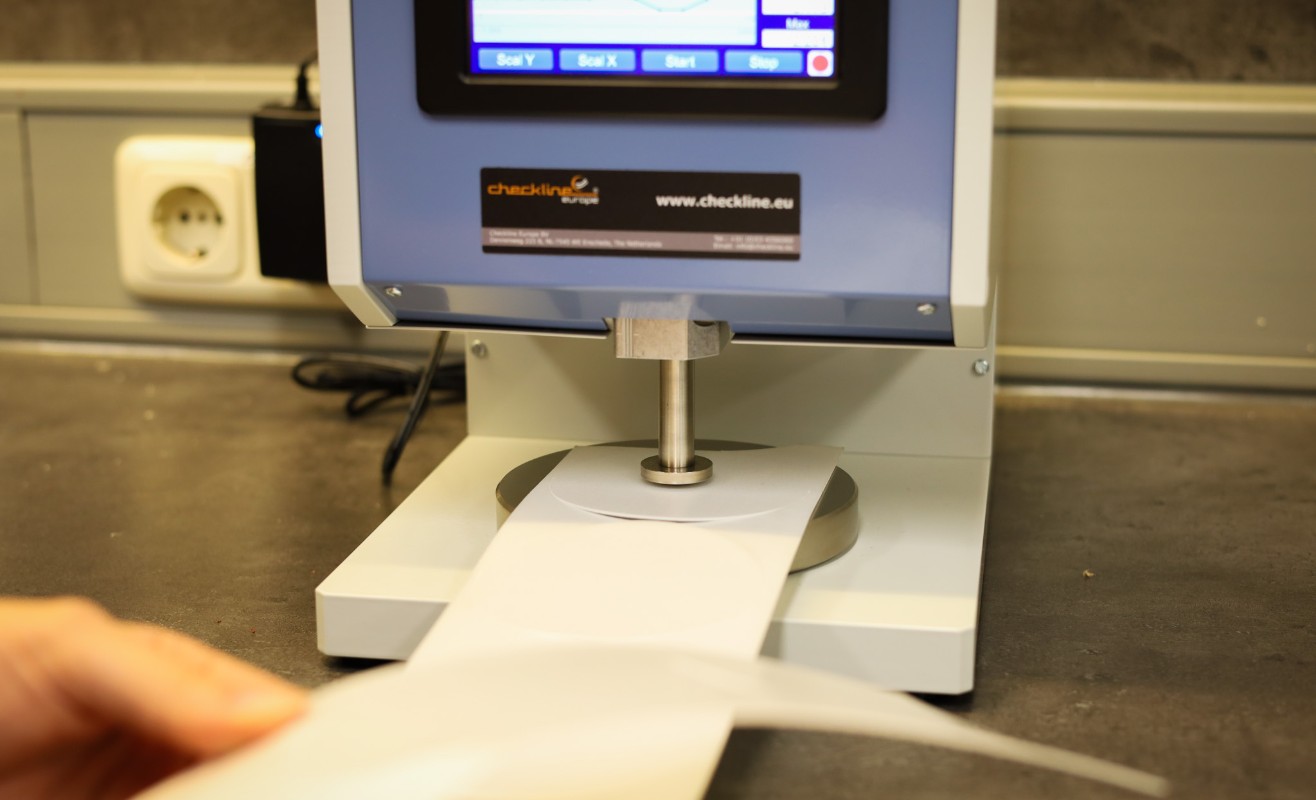
Sustainability through mono-materials
Kornelis is working on several projects to make their products more sustainable. One important step is using ultrasonic welding to attach the polypropylene (PP) insert inside a PP lid. "We used to use hotmelt glue, but that’s no longer needed," Mireia explains. "Now we have a fully mono-PP lid, which is much easier to recycle."
Another example is replacing the cardboard tagger—the backing of the insert—with a version made of foamed polypropylene. "Consumers often don’t remove the cardboard, which means mixed materials end up in the recycling stream," Mireia says. "Using a fully PP tagger solves this problem."
Regulations as a driving force
European food regulations 10/2011 and the upcoming Packaging and Packaging Waste Regulation (PPWR) guide many of these changes. Over the past years, Kornelis has reviewed and improved all their formulas. "For example, we replaced the oil previously used with powdered lubricant by a lubricant with a PP carrier that has similar properties," Mireia says. "This helps us control the composition and meet future requirements." Peter adds, "Thanks to better mold coatings and servo-controlled machines, we need fewer additives overall. Every step helps us move closer to mono-material products."
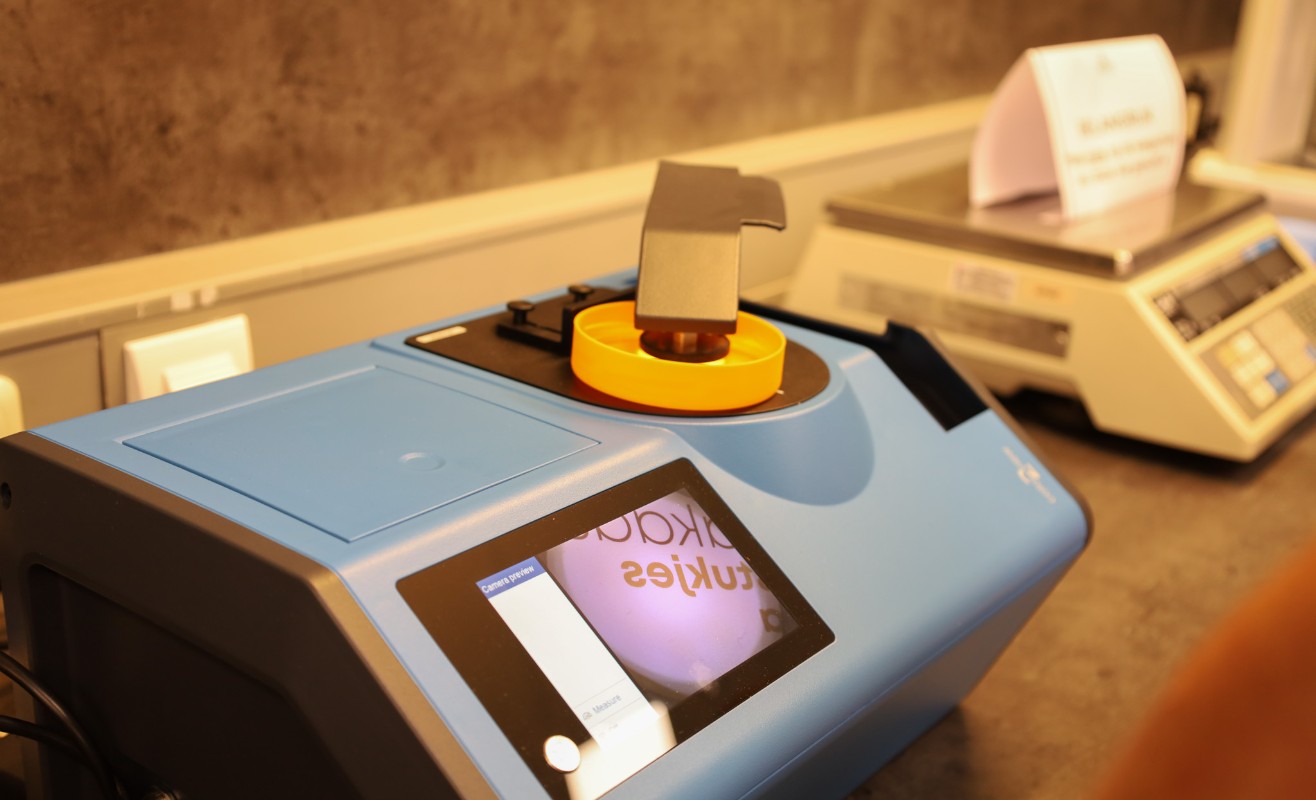
Biobased materials
Although Kornelis can process biobased plastics, the market isn’t quite ready yet. "Customers do ask for it, but when it comes to paying more, they often back out," says Mireia. Still, preparations are underway. Kornelis is ISCC Plus certified and is working on an EcoVadis sustainability rating. "We want to be ready as soon as the market accepts it."
The lab as a hub for innovation
With the upgraded lab as their foundation, Kornelis is steadily working toward a future where data-driven production, process optimization, and sustainability come together. Peter sums it up: "We want to be able to measure, understand, and improve everything. That’s the only way to make real progress."